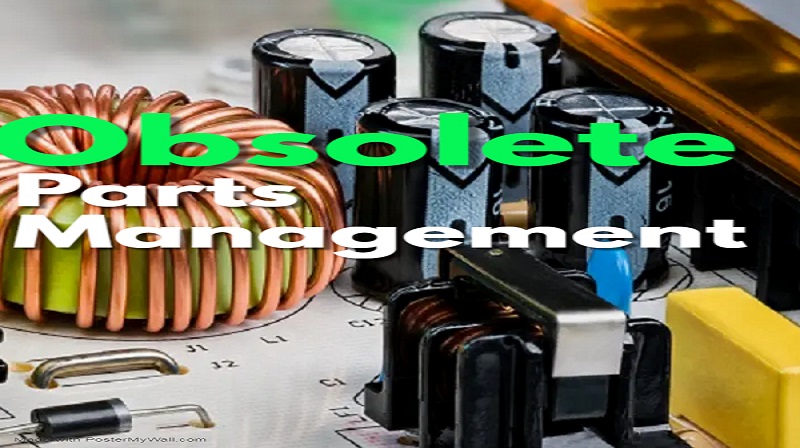
Obsolete Parts Management
- by PLC
- Mar 16, 2023
Obsolete parts management refers to the process of managing and disposing of parts that are no longer needed or in use. This process is essential for businesses that rely on complex machinery and equipment that require regular maintenance and repairs. Failure to manage obsolete parts can lead to inefficiencies, increased costs, and potential safety hazards. In this article, we will explore the importance of obsolete parts management and strategies for effective management.
Importance of Obsolete Parts Management:
Obsolete parts can be defined as parts that are no longer being manufactured or used in new equipment. They may become obsolete due to advancements in technology, changes in industry standards, or the discontinuation of specific products or models. The importance of obsolete parts management lies in the fact that it helps businesses to:
Reduce Costs: By identifying and removing obsolete parts from inventory, businesses can reduce the cost of storing and managing these parts. They can also avoid the cost of purchasing replacement parts that are no longer needed.
Optimize Inventory: Obsolete parts can take up valuable space in the inventory, making it difficult to manage and organize. By removing these parts, businesses can optimize their inventory and make room for more critical parts and supplies.
Increase Efficiency: By having an organized and up-to-date inventory, businesses can reduce the time and resources needed to locate and retrieve parts. This can increase competence and reduce downtime.
Improve Safety: Obsolete parts can pose safety hazards if they are used in repairs or maintenance. By managing and disposing of these parts properly, businesses can ensure that their equipment is maintained to the highest safety standards.
Strategies for Effective Obsolete Parts Management
Inventory Analysis: Regular inventory analysis is essential for identifying obsolete parts. This analysis should include a review of usage rates, lead times, and supplier information.
Disposition Planning: Once obsolete parts have been identified, a disposition plan should be developed. This plan should include options for disposing of the parts, such as selling, scrapping, or donating.
Replacement Planning: Replacement planning involves identifying alternative parts that can be used in place of obsolete parts. This planning should take into consideration the availability and cost of replacement parts.
Communication: Effective communication between the maintenance and purchasing departments is critical for managing obsolete parts. The maintenance department should communicate any issues or concerns with obsolete parts to the purchasing department, which can then take appropriate action.
In conclusion, obsolete parts management is a critical process for businesses that rely on complex machinery and equipment. Effective management can help businesses reduce costs, optimize inventory, increase efficiency, and improve safety. By implementing strategies such as inventory analysis, disposition planning, replacement planning, and effective communication, we at PLC Automation PTE Ltd try to effectively manage the obsolete parts and ensure that our equipments are maintained to the highest standards.