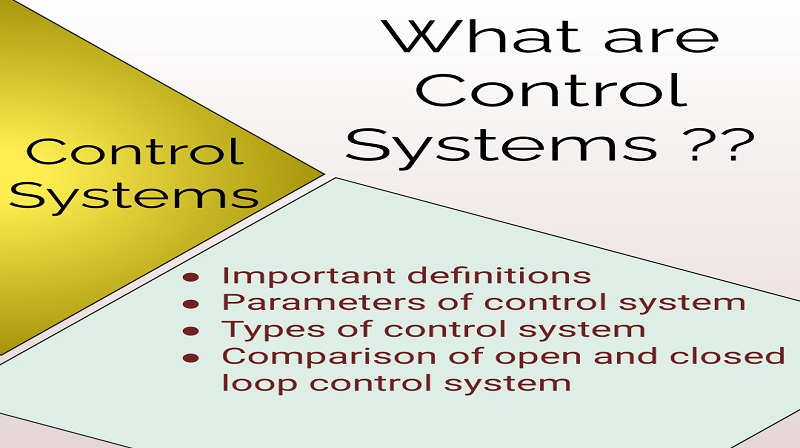
Control System
- by PLC
- Mar 24, 2023
Control systems are essential tools used in various fields, including engineering, manufacturing, and even everyday life. They help in regulating and manage complex processes, ensuring that they operate smoothly and efficiently. There are several types of control systems, each with unique features and applications. In this blog, we will discuss the most common types of control systems. Each category contains specific parameters that define the behavior and performance of the control system. In this blog, we will discuss the parameters of control systems.
Input Parameters
The input parameters of a control system refer to the signals or data that enter the system. They include:
- Setpoint: The desired value or reference point that the control system aims to achieve.
- Process variable: The actual value of the process being controlled.
- Disturbance: Any external factor that affects the process being controlled.
- Noise: Any unwanted signal or interference that affects the accuracy of the control system.
Processing Parameters
The processing parameters of a control system refer to the components and algorithms that process the input signals to produce the desired output. They include:
- Controller gain: The factor that determines the strength of the control signal.Proportional, Integral, and Derivative (PID) parameters: The coefficients that determine the control action in a PID controller.
- Time constants: The time it takes for the control system to respond to changes in the input signals.
- Sampling rate: The rate at which the control system measures the input signals and produces output signals.
Output Parameters
The output parameters of a control system refer to the signals or data that the system produces. They include:
- Control signal: The signal that the control system sends to the process to adjust its behavior.
- Output signal: The signal that the control system produces is based on the input signals and processing parameters.
- Error signal: The difference between the setpoint and the process variable.
- Control action: The action taken by the control system to regulate the process and minimize the error signal.
TYPES OF CONTROL SYSTEM
1. Open-Loop Control Systems
An open-loop control system is a type of system that operates based on predetermined instructions. It means that the output of the system does not affect the input. For example, a washing machine set to run for 30 minutes will stop after 30 minutes, regardless of whether the clothes are clean or not. Open-loop control systems are simple and cost-effective, but they are not suitable for processes that require constant monitoring and adjustment.
2. Closed-Loop Control Systems
A closed-loop control system is a type of system that uses feedback to adjust its output. The output of the system affects the input, which means that the system can make corrections based on the feedback it receives. For example, a thermostat uses a closed-loop control system to regulate the temperature in a room. It senses the temperature and adjusts the heating or cooling system accordingly. Closed-loop control systems are more complex than open-loop control systems, but they are more accurate and reliable.
3. Linear Control Systems
A linear control system is a type of system that uses linear equations to model its behavior. It means that the relationship between the input and output of the system is linear. For example, a system that regulates the speed of a motor based on the voltage applied to it is a linear control system. Linear control systems are relatively easy to model and analyze, making them popular in control engineering.
4. Nonlinear Control Systems
A nonlinear control system is a type of system that uses nonlinear equations to model its behavior. It means that the relationship between the input and output of the system is nonlinear. Nonlinear control systems are more complex than linear control systems, but they can model and control processes that linear systems cannot.
5. On-Off Control Systems
An on-off control system is a type of system that switches between two states based on a threshold. For example, a thermostat that turns a heating system on when the temperature falls below a certain threshold and turns it off when it reaches another threshold is an on-off control system. On-off control systems are simple and cost-effective, but they are not suitable for processes that require fine-tuning or precise control.
COMPARISON BETWEEN OPEN AND CLOSED LOOP CONTROL SYSTEM
Open and closed-loop control systems are two types of control systems used in various applications, including manufacturing, engineering, and automation. They differ in their functionality, complexity, and performance. In this blog, we will discuss the differences between open and closed-loop control systems.
A. Functionality:
Open-loop control systems are simple and operate based on predetermined instructions. The input to the system is not affected by the output, which means that the system does not use feedback to adjust its behavior. In contrast, closed-loop control systems use feedback to adjust their behavior based on the output. The input to the system is affected by the output, which means that the system can make corrections based on the feedback it receives.
B. Complexity:
Open loop control systems are relatively simple and cost-effective. They do not require feedback mechanisms, which means that they are easy to design and implement. In contrast, closed-loop control systems are more complex and expensive. They require feedback mechanisms, such as sensors, controllers, and actuators, which means that they are more challenging to design and implement.
C. Performance:
Open-loop control systems are less accurate and reliable than closed-loop control systems. They do not use feedback to adjust their behavior, which means that they are susceptible to disturbances and variations in the process being controlled. In contrast, closed-loop control systems are more accurate and reliable. They use feedback to adjust their behavior, which means that they can compensate for disturbances and variations in the process being controlled.
Applications:
Open loop control systems are commonly used in simple applications that do not require fine-tuning or precise control. For example, a washing machine with a timer is an open-loop control system. Closed-loop control systems are used in more complex applications that require accurate and reliable control. For example, a temperature control system in a furnace is a closed-loop control system.
In conclusion, control systems are essential tools used in various fields to regulate and manage complex processes. The most common types of control systems are open-loop, closed-loop, linear, nonlinear, and on-off control systems. Each type has its unique features and applications, and selecting the right type for a particular process is critical to achieving optimal performance. control systems consist of input, processing, and output parameters that define their behavior and performance. Understanding these parameters is crucial in designing, implementing, and optimizing control systems for various applications. open loop and closed-loop control systems differ in their functionality, complexity, and performance. Open-loop control systems are simple and operate based on predetermined instructions, while closed-loop control systems use feedback to adjust their behavior based on the output. Open-loop control systems are less accurate and reliable than closed-loop control systems and are commonly used in simple applications, while closed-loop control systems are used in more complex applications that require accurate and reliable control. By carefully selecting and tuning these parameters, engineers and operators at PLC Automation PTE LTD ensure that control systems operate effectively and efficiently.