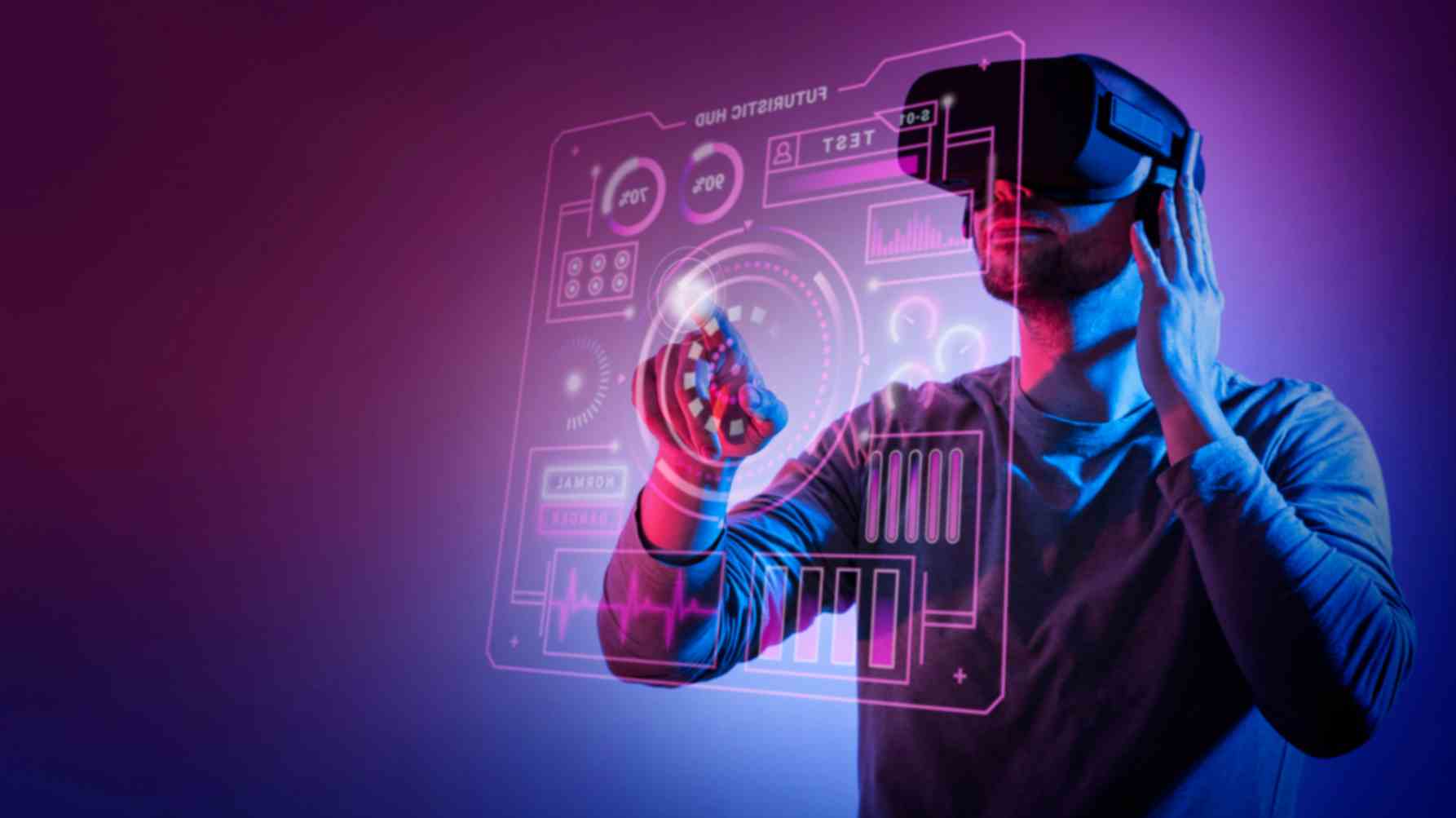
Navigating the Digital Transformation A Guide for Small Manufacturers
- by PLC
- Oct 01, 2023
Introduction
The integration of digital technology has become a revolutionary force for manufacturers of all sizes in today's fast shifting industrial scene. Small enterprises, in particular, must embrace the digital revolution in order to remain competitive and survive in a volatile market. This article explores the pivotal role of digital technologies in manufacturing and delves into the unique benefits they offer to small-scale manufacturers. From understanding the core concepts of digital transformation to practical strategies and case studies, we will navigate the journey of how small manufacturers can harness the power of digital technologies to streamline operations, enhance productivity, and secure a prosperous future.
Section 1: Understanding Digital Technologies
In the realm of manufacturing, digital technologies encompass a broad spectrum of innovations and tools designed to optimize processes, enhance efficiency, and deliver superior results. At its core, digital technology in manufacturing refers to the integration of digital systems, data-driven approaches, and automation solutions to streamline operations.
One of the key pillars of digital transformation is the Internet of Things (IoT), which enables the connectivity of physical devices and machines through the internet. IoT empowers manufacturers with real-time data collection, remote monitoring, and predictive maintenance, fostering proactive decision-making and reducing downtime.
Artificial Intelligence (AI) plays a pivotal role by providing machines with the ability to learn, analyze vast datasets, and make intelligent decisions. AI-driven algorithms optimize production, quality control, and supply chain management, driving accuracy and cost-effectiveness.
Automation, another integral component, eliminates manual tasks, enhances precision, and boosts productivity. Robotics, autonomous systems, and robotic process automation (RPA) contribute to increased efficiency and consistency.
Embracing these digital technologies yields an array of benefits for small manufacturers. Improved operational efficiency leads to reduced production costs and shorter lead times. Enhanced product quality and consistency result in higher customer satisfaction and loyalty. Moreover, the data-driven insights derived from these technologies enable manufacturers to make informed decisions, adapt to market fluctuations, and maintain a competitive edge in today's fast-paced manufacturing landscape.
Section 2: Assessing Your Current State
Before embarking on the journey of digital transformation, small manufacturers must first take stock of their current technological landscape. This assessment serves as the foundation for informed decision-making and successful integration of digital technologies.
Assessing the existing technology infrastructure involves evaluating the hardware, software, and systems currently in use within the manufacturing facility. This examination helps identify any outdated or incompatible technologies that may hinder the adoption of digital solutions.
Equally important is gaining a deep understanding of the current manufacturing processes and challenges. This step allows manufacturers to pinpoint areas where digital technologies can make the most significant impact. It also helps in setting clear objectives and priorities for the digital transformation journey.
Moreover, by comprehending the challenges and pain points faced in day-to-day operations, manufacturers can tailor their digital solutions to address these specific issues. Whether it's improving production efficiency, reducing waste, or enhancing quality control, a thorough assessment provides the essential insights needed to align digital strategies with business goals.
Section 3: Setting Clear Objectives
In the realm of digital transformation for small manufacturers, setting clear and specific objectives is akin to charting a course on a complex journey. These objectives serve as the guiding stars that illuminate the path toward a successful digital transformation effort.
First and foremost, specific objectives provide clarity and focus. They define the outcomes that a manufacturer seeks to achieve through digital technologies. For example, an objective may be to "increase production efficiency by 20% within the next year." This specific target allows for a tangible and measurable goal.
Common objectives in digital transformation often revolve around key performance indicators (KPIs) such as increased efficiency, reduced operational costs, and improved product quality.
- Increased Efficiency: Manufacturers may aim to optimize production processes, reduce cycle times, or minimize downtime through real-time monitoring and predictive maintenance.
- Reduced Costs: Cost reduction objectives can involve lowering energy consumption, optimizing resource allocation, and minimizing waste.
- Improved Quality: Enhancing product quality and consistency is a frequent goal, achieved through precision control and data-driven quality assurance.
By establishing these clear objectives, small manufacturers not only align their digital transformation efforts with business goals but also create a roadmap for implementation. It ensures that every technological investment and strategic decision made throughout the transformation process contributes directly to the achievement of these objectives.
Section 4: Planning Your Digital Transformation
Creating a digital transformation roadmap is an essential step in ensuring the successful adoption of digital technologies by small manufacturers. It serves as a strategic blueprint that outlines the journey from the current state to the desired future state, all while considering key factors like technology investments, budgeting, and resource allocation.
A digital transformation roadmap provides a structured approach to the integration of digital technologies. It identifies the specific technologies and solutions that will be implemented and the timeline for their adoption. This roadmap serves as a guiding document, helping manufacturers stay on track and prioritize actions that align with their overarching objectives.
Prioritizing technology investments is crucial for small manufacturers with limited resources. By assessing the potential impact and alignment with objectives, manufacturers can determine which technologies should be implemented first. This prioritization ensures that investments are made where they can deliver the most significant return on investment (ROI).
Budgeting and resource allocation are paramount in the planning phase. Manufacturers need to allocate sufficient funds and resources to support technology adoption, training, and ongoing maintenance. Clear budgetary planning helps prevent unexpected expenses and ensures that the digital transformation remains on course.
Section 5: Selecting the Right Technologies
Choosing the right digital technologies for your small manufacturing business is a critical decision that can impact your success in the digital transformation journey. To make informed choices, consider several factors:
- Scalability: Opt for technologies that can grow with your business. Ensure they can handle increased demand as your manufacturing operations expand.
- Compatibility: Assess how well the chosen technologies integrate with your existing systems. Compatibility minimizes disruptions during implementation.
- Industry-Specific Needs: Recognize that each industry has unique requirements. Select technologies that address specific challenges and opportunities within your sector.
- ROI Potential: Evaluate the potential return on investment (ROI) for each technology. Focus on solutions that offer the most significant ROI aligned with your objectives.
- Ease of Adoption: Choose technologies that are user-friendly and provide adequate training and support. User adoption is crucial for success.
By carefully considering these factors, small manufacturers can make informed decisions when selecting technologies that best fit their business needs and digital transformation goals.
Section 6: Implementation and Integration
Implementing digital technologies in small manufacturing requires a structured approach:
- Assessment: Begin with a comprehensive assessment of your current systems and processes.
- Strategy: Develop a clear strategy and timeline for implementation, aligning with your objectives.
- Technology Selection: Choose the right technologies and solutions based on your needs.
- Pilot Testing: Conduct pilot tests to identify and resolve issues on a smaller scale.
- Integration: Seamlessly integrate new technologies with existing systems to ensure data flow and functionality.
- Training: Provide training to employees for effective adoption.
Challenges like resistance to change and potential disruptions can be addressed through communication, change management strategies, and ongoing support. The key to successful implementation is a well-executed plan that minimizes downtime and maximizes the benefits of digital transformation.
Section 7: Employee Training and Change Management
Employee training is a cornerstone of successful digital transformation in small manufacturing. It empowers your workforce to effectively utilize new technologies and adapt to evolving processes.
Change management strategies are vital to facilitate a seamless transition. These include:
- Clear Communication: Keep employees informed about the transformation's purpose and benefits.
- Inclusive Approach: Involve employees in decision-making and seek their input.
- Training Programs: Provide comprehensive training programs tailored to different roles and skill levels.
- Support Systems: Offer ongoing support and resources to address questions and concerns.
- Feedback Loops: Establish feedback mechanisms to continuously refine and improve the transformation process.
By prioritizing training and implementing change management strategies, small manufacturers can foster a culture of adaptation and innovation, ensuring a smooth transition to digital technologies.
Section 8: Measuring and Monitoring Progress
Tracking key performance indicators (KPIs) is paramount in gauging the success of digital transformation efforts for small manufacturers. KPIs provide quantifiable metrics to evaluate the impact of digital technologies on various aspects of the business.
Data analytics plays a pivotal role in this process, as it allows for in-depth assessment and insights derived from real-time data. Manufacturers can measure factors like increased efficiency, reduced costs, improved product quality, and enhanced customer satisfaction. These insights guide decision-making, helping refine strategies and ensuring that the digital transformation remains aligned with the business's overarching objectives.
Section 9: Case Studies
Real-world case studies demonstrate the tangible benefits of digital transformation for small manufacturers:
- Case Study 1: Precision Engineering Co.: This small manufacturer adopted IoT sensors to monitor machine health. As a result, they reduced unplanned downtime by 30%, boosting production efficiency.
- Case Study 2: Quality Plastics Inc.: By implementing AI-driven quality control systems, this manufacturer improved product quality and reduced defects by 20%, leading to increased customer satisfaction and higher demand.
- Case Study 3: Craft Metalworks: Automation of inventory management using digital technologies resulted in a 25% reduction in operational costs and improved supply chain efficiency.
These cases illustrate how digital technologies can drive efficiency, quality, and cost-effectiveness, ultimately enhancing competitiveness and profitability for small manufacturers.
Conclusion
In conclusion, the digital transformation journey for small manufacturers is laden with opportunities for growth, efficiency, and competitiveness. By understanding, planning, and implementing the right technologies, businesses can achieve their objectives, whether that's increased efficiency, reduced costs, or improved product quality.
Embracing digital technologies isn't just a choice; it's a necessity to thrive in the evolving landscape of manufacturing. As technology continues to advance, those who adapt will gain a competitive edge, while those who resist risk falling behind. The future of manufacturing is digital, and it promises a world of possibilities for small manufacturers willing to embark on this transformative journey.