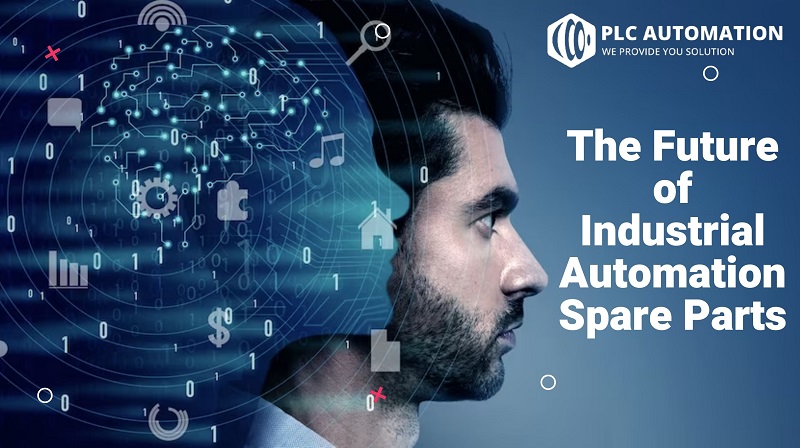
PLC Automation Pte Ltd is the Future of Industrial Automation Spare Parts
- by PLC
- Oct 02, 2023
Industrial automation has revolutionized manufacturing and production processes over the years, increasing efficiency, reducing errors, and lowering operational costs. As automation technologies continue to advance, the role of spare parts in industrial automation systems is undergoing a transformation. In this blog, we will explore the future of industrial automation spare parts, highlighting the innovations and trends that are shaping this crucial aspect of modern manufacturing.
1. Predictive Maintenance and Spare Parts Optimization
One of the most significant advancements in the industrial automation spare parts sector is the integration of predictive maintenance algorithms. These algorithms analyze real-time data from sensors and equipment to predict when a component is likely to fail. This proactive approach enables companies to order spare parts only when needed, reducing inventory costs and minimizing downtime. It's a game-changer in terms of cost-efficiency and operational continuity.
Predictive Maintenance: Anticipating Issues Before They Occur
Predictive maintenance is all about using data and analytics to predict when equipment is likely to fail so that maintenance can be performed just in time. Here's how it works:
- Data Collection: Sensors and monitoring devices are installed on critical equipment and machinery. These sensors continuously collect data on various parameters, such as temperature, vibration, pressure, and more. This data is then transmitted to a central system for analysis.
- Data Analysis: In the central system, powerful algorithms and machine learning models process the incoming data. These models look for patterns and anomalies that might indicate potential issues or wear and tear in the machinery.
- Predictive Alerts: When the algorithms detect anomalies or patterns indicative of a problem, they trigger alerts. Maintenance teams receive these alerts, and they can take proactive action, scheduling maintenance when it's most convenient and cost-effective.
Advantages of Predictive Maintenance:
- Reduced Downtime: By addressing issues before they lead to breakdowns, predictive maintenance minimizes unplanned downtime, increasing overall equipment effectiveness (OEE).
- Lower Costs: Maintenance activities are targeted and efficient, reducing the need for frequent and costly preventive maintenance.
- Extended Equipment Lifespan: Predictive maintenance helps optimize the life of equipment by addressing problems early, preventing excessive wear and tear.
Spare Parts Optimization: A Key Component
To make the most of predictive maintenance, spare parts optimization is essential. This involves ensuring that the right spare parts are available when needed, without overstocking or understocking. Here's how it complements predictive maintenance:
- Inventory Management: An intelligent spare parts management system takes into account the predictions made by the maintenance algorithms. It maintains an up-to-date inventory of spare parts based on the likelihood of equipment failures.
- Supplier Relationships: Companies establish strong relationships with reliable suppliers to ensure quick access to spare parts. This can include just-in-time delivery agreements and emergency response protocols.
- Cost Efficiency: By stocking only the necessary spare parts and reducing the risk of last-minute, expensive orders, companies can significantly cut down on maintenance costs.
- Data-Driven Decision Making: Spare parts optimization relies on data analytics, just like predictive maintenance. It ensures that the right parts are available at the right time, further minimizing downtime.
The Synergy Between Predictive Maintenance and Spare Parts Optimization
The integration of predictive maintenance and spare parts optimization is where the real magic happens. By combining these strategies:
- Companies can confidently schedule maintenance activities, knowing they have the required spare parts on hand.
- Emergency spare parts orders become rare exceptions rather than the norm, saving time and money.
- Inventory carrying costs are reduced as spare parts are used efficiently, contributing to cost savings.
In conclusion, predictive maintenance and spare parts optimization represent a forward-looking approach to industrial efficiency. They harness the power of data and technology to ensure that equipment keeps running smoothly while minimizing operational costs. As industries continue to embrace these strategies, they'll be better equipped to thrive in an increasingly competitive and demanding manufacturing landscape.
2. 3D Printing for Spare Parts
3D printing technology is gaining ground in the manufacturing industry, including the production of spare parts. Manufacturers can now produce custom spare parts on-demand using 3D printers, eliminating the need for large inventories of pre-made parts. This not only reduces storage costs but also enables quicker response times when replacements are required. As 3D printing technology continues to evolve, it will play a more prominent role in the future of industrial automation spare parts.
How 3D Printing Works for Spare Parts
3D printing, also known as additive manufacturing, is a process in which a three-dimensional object is created layer by layer from a digital model. Here's how 3D printing technology can be applied to the production of spare parts:
- Digital Design: The process begins with the creation of a 3D digital model of the required spare part. This model serves as the blueprint for the 3D printer.
- Layer-by-Layer Printing: The 3D printer reads the digital model and prints the spare part layer by layer using various materials such as plastics, metals, ceramics, or composites.
- Quality Control: Once the printing is complete, the spare part is carefully inspected for quality and accuracy. Post-processing steps like sanding, polishing, or surface treatment may be applied to ensure the part meets the desired specifications.
- Ready for Use: After passing quality control checks, the spare part is ready for use or installation in the industrial equipment.
Benefits of 3D Printing for Spare Parts
The adoption of 3D printing for spare parts offers numerous advantages:
- Reduced Lead Times: 3D printing allows for rapid prototyping and production, significantly reducing lead times compared to traditional manufacturing methods.
- Cost-Efficiency: Traditional manufacturing often requires expensive molds, tooling, and minimum order quantities. 3D printing eliminates these constraints, enabling cost-effective production of low-volume spare parts.
- Customization: 3D printing allows for easy customization of spare parts to match specific equipment requirements or modifications.
- Reduced Inventory Costs: Companies can reduce their spare parts inventories as they shift to on-demand 3D printing. This results in lower storage costs and less capital tied up in spare parts.
- Sustainability: 3D printing generates minimal waste compared to subtractive manufacturing methods, making it an eco-friendly option.
Applications of 3D Printing in Spare Parts
The applications of 3D printing for spare parts are vast and cover a wide range of industries:
- Aerospace: Airlines and aerospace companies use 3D printing to produce complex and lightweight spare parts for aircraft.
- Automotive: Car manufacturers employ 3D printing to create customized spare parts for vehicles.
- Medical: Hospitals and medical device companies utilize 3D printing to manufacture patient-specific replacement parts for medical equipment.
- Manufacturing: Factories and industrial facilities rely on 3D printing to produce spare parts for machinery and equipment, reducing downtime.
- Consumer Goods: Manufacturers of consumer electronics and appliances can quickly produce spare parts for repairs and maintenance.
In conclusion, 3D printing for spare parts represents a revolutionary shift in the way we think about manufacturing and maintenance. It offers agility, cost-efficiency, and customization, making it a vital tool in modern industrial operations. As 3D printing technology continues to advance, its role in the world of spare parts production will only become more significant, helping industries reduce downtime and maintain their competitive edge.
3. IoT-Enabled Spare Parts
The Internet of Things (IoT) has already transformed the industrial landscape, and its influence on spare parts is undeniable. IoT-enabled spare parts come equipped with sensors and communication capabilities that allow them to transmit real-time data about their condition and usage. This data helps in monitoring the health of spare parts, enabling proactive maintenance and reducing unexpected breakdowns.
Key Features and Benefits:
- Real-Time Monitoring: IoT-enabled spare parts continuously monitor their own health and performance. For example, a sensor in a bearing can track temperature, vibration, and lubrication levels. This real-time data helps identify early signs of wear or potential failure.
- Predictive Maintenance: By analyzing the data from IoT-enabled spare parts, maintenance teams can predict when a component is likely to fail. This enables proactive maintenance scheduling, reducing unplanned downtime and optimizing maintenance costs.
- Condition-Based Replacement: IoT-enabled spare parts can communicate their condition to maintenance systems. When a spare part reaches a predefined threshold indicating that it needs replacement or servicing, an alert is generated, prompting timely action.
- Inventory Optimization: IoT data helps in optimizing spare parts inventory. Instead of stocking a surplus of spare parts, companies can maintain just-in-time inventory levels based on real usage and wear data.
- Enhanced Reliability: With the ability to monitor spare parts in real time, industrial equipment can operate with greater reliability and reduced risk of unexpected breakdowns.
Applications Across Industries:
- Manufacturing: IoT-enabled spare parts are used in manufacturing plants to monitor and maintain critical machinery. For instance, in a factory, sensors embedded in conveyor belts can track wear and tear, ensuring timely replacement before a breakdown occurs.
- Energy: In the energy sector, IoT-enabled spare parts are deployed in power generation equipment to optimize performance and extend the lifespan of components.
- Transportation: Airlines and railways use IoT-enabled spare parts in aircraft and trains to enhance safety, improve maintenance, and reduce operational disruptions.
- Healthcare: Hospitals rely on IoT-enabled spare parts in medical devices to ensure they function optimally. For example, sensors in MRI machines can detect anomalies in key components.
- Utilities: Utilities providers employ IoT-enabled spare parts in infrastructure maintenance, such as monitoring the condition of water pumps and electrical transformers.
Challenges and Considerations:
While IoT-enabled spare parts offer substantial benefits, they also come with challenges, including data security, interoperability, and the need for specialized skills to manage IoT systems. Additionally, there are considerations regarding the cost of implementing IoT technology and ensuring compatibility with existing equipment. IoT-enabled spare parts are a vital component of the industrial IoT ecosystem, poised to revolutionize maintenance practices across industries. As technology continues to advance and the cost of IoT adoption decreases, we can expect to see even greater integration of these smart spare parts into industrial processes, leading to increased efficiency, reduced costs, and enhanced reliability in the world of automation.
4. Artificial Intelligence in Spare Parts Management
Artificial intelligence (AI) is making significant inroads into spare parts management. AI-driven algorithms can predict spare parts requirements, optimize inventory levels, and even suggest alternative components when specific parts are unavailable. This not only streamlines spare parts procurement but also helps companies make more informed decisions regarding their spare parts strategies.
AI-Powered Spare Parts Management
AI in spare parts management involves the use of machine learning algorithms and data analysis to make informed decisions about the procurement, stocking, and maintenance of spare parts. Here's how AI is making a significant impact:
- Demand Forecasting: AI algorithms can analyze historical usage data, equipment performance data, and other relevant factors to predict future demand for spare parts accurately. This enables organizations to maintain optimal inventory levels and reduce the risk of understocking or overstocking.
- Predictive Maintenance: AI-powered predictive maintenance systems can anticipate when a machine or component is likely to fail. These systems can also predict which spare parts will be needed for specific maintenance tasks, ensuring that the right parts are available when required.
- Inventory Optimization: AI-driven algorithms continuously assess spare parts inventory to optimize stocking levels. This leads to cost savings by reducing excess inventory carrying costs while ensuring critical parts are always on hand.
- Supplier Performance Monitoring: AI can monitor supplier performance by analyzing data related to delivery times, part quality, and pricing. This information helps in selecting and managing suppliers more effectively.
- Dynamic Pricing: AI can analyze market conditions, supplier quotes, and historical pricing data to negotiate better prices for spare parts, resulting in cost savings.
- Failure Mode Analysis: AI can analyze equipment data to identify patterns of failure. This helps organizations proactively address recurring issues by stocking the right spare parts and performing preventive maintenance.
Benefits of AI in Spare Parts Management
The integration of AI into spare parts management offers several key benefits:
- Reduced Downtime: AI's predictive capabilities help organizations avoid unplanned downtime by ensuring that the right spare parts are available when needed.
- Cost Reduction: Improved inventory management and pricing optimization lead to significant cost savings.
- Enhanced Efficiency: AI automates many aspects of spare parts management, reducing the manual workload and potential for human error.
- Improved Decision-Making: AI provides actionable insights and recommendations, empowering organizations to make data-driven decisions.
- Better Customer Satisfaction: With fewer production interruptions due to spare parts availability, organizations can meet customer demands more effectively.
Challenges and Considerations
While AI brings tremendous advantages to spare parts management, there are challenges to consider. These include the need for high-quality data, integration with existing systems, the cost of AI implementation, and ensuring that staff have the necessary skills to work with AI-powered tools. Artificial Intelligence is transforming spare parts management from a reactive, manual process into a proactive, data-driven discipline. By harnessing the power of AI, organizations can optimize inventory, reduce downtime, lower costs, and improve overall operational efficiency. As AI technology continues to evolve, its role in spare parts management will only become more central to ensuring the smooth operation of industries worldwide.
5. Blockchain for Spare Parts Traceability
Blockchain technology is gaining traction for its ability to provide transparency and traceability in supply chains. In the context of industrial automation spare parts, blockchain can be used to create a secure and immutable ledger of spare parts transactions. This ensures the authenticity of spare parts and reduces the risk of counterfeit components entering the supply chain, thereby enhancing the reliability and safety of automation systems.
How Blockchain Works in Spare Parts Traceability
Blockchain is a distributed ledger technology that records transactions across multiple computers in a way that is secure, transparent, and tamper-proof. Here's how it is applied to spare parts traceability:
- Digital Identities: Each spare part is assigned a unique digital identity on the blockchain. This identity can include details such as the part's manufacturer, production date, serial number, and relevant certifications.
- Immutable Records: Information about the spare part's journey through the supply chain is recorded as transactions on the blockchain. Once added, these records cannot be altered or deleted, ensuring the integrity of the data.
- Smart Contracts: Smart contracts are self-executing contracts with predefined rules and conditions. In spare parts traceability, smart contracts can automate processes such as quality inspections, certifications, and payment releases when specific conditions are met.
- Transparency: All stakeholders in the supply chain, from manufacturers and distributors to end-users, can access the blockchain to verify the authenticity and history of spare parts. This transparency fosters trust among participants.
Benefits of Blockchain in Spare Parts Traceability
- Counterfeit Prevention: Blockchain's immutability ensures that once a spare part is registered on the ledger, it cannot be counterfeited or replaced with a counterfeit part, enhancing authenticity.
- Quality Assurance: Information about quality control checks, certifications, and testing results is securely recorded on the blockchain, assuring the quality of spare parts.
- Improved Recalls: In the event of a recall, blockchain enables swift identification of affected parts, reducing the time and cost of recall procedures.
- Reduced Fraud: Blockchain's transparency and security make it difficult for bad actors to engage in fraudulent activities, such as selling counterfeit or substandard parts.
- Supply Chain Optimization: By providing real-time visibility into the movement of spare parts, blockchain can optimize supply chain logistics, reducing lead times and minimizing delays.
- Enhanced Warranty Management: Manufacturers can use blockchain to track the warranty status of spare parts, making it easier to identify parts still under warranty and those that require payment for repairs or replacements.
Applications Across Industries
Blockchain for spare parts traceability has broad applications across various industries, including:
- Automotive: Ensuring the authenticity and traceability of automotive spare parts is crucial for safety and performance.
- Aerospace: The aerospace industry relies on blockchain to trace critical components in aircraft to comply with stringent safety and maintenance regulations.
- Healthcare: Medical equipment and devices depend on blockchain for traceability to guarantee patient safety.
- Manufacturing: Manufacturers across industries use blockchain to track spare parts in their production and assembly processes.
Challenges and Considerations
While blockchain offers significant benefits, its adoption in spare parts traceability faces challenges, including cost, scalability, standardization, and the need for industry-wide collaboration.
Blockchain technology is revolutionizing spare parts traceability by providing a secure, transparent, and tamper-proof system for recording and verifying spare part information. As industries increasingly recognize the importance of authentic and reliable spare parts, blockchain's role in supply chain management and spare parts traceability will continue to grow, ensuring safety, reliability, and trust in critical equipment and machinery.
6. Remote Diagnostics and Troubleshooting
The rise of remote monitoring and diagnostics tools is transforming the way spare parts are managed. Automation systems equipped with remote access capabilities can be diagnosed and troubleshot from anywhere in the world, often negating the need for physical spare parts to be shipped. This trend not only reduces downtime but also lowers transportation costs and carbon emissions.
Understanding Remote Diagnostics and Troubleshooting
Remote diagnostics and troubleshooting involve the use of technology and connectivity to monitor, diagnose, and address issues in industrial automation systems and machinery from a distance. Here's how it works:
- Sensor Data Collection: Sensors and data acquisition systems are integrated into industrial equipment. These sensors collect real-time data on various parameters such as temperature, pressure, vibration, and performance.
- Data Transmission: The collected data is transmitted to a central monitoring system or the cloud in real time. This data can be accessed remotely by technicians, engineers, or AI-powered systems.
- Data Analysis: Advanced analytics and artificial intelligence algorithms analyze the data to identify anomalies, trends, and potential issues. These algorithms can detect deviations from normal operating conditions.
- Remote Alerts: When an issue is detected, the system generates alerts or notifications. Technicians or maintenance teams can receive these alerts on their devices, allowing them to respond quickly.
- Remote Access: In some cases, remote access tools enable technicians to access and control equipment from afar. They can troubleshoot, make adjustments, or perform maintenance tasks remotely.
Benefits of Remote Diagnostics and Troubleshooting
The adoption of remote diagnostics and troubleshooting offers several significant advantages:
- Reduced Downtime: Quick identification and resolution of issues minimize equipment downtime, leading to increased productivity and cost savings.
- Lower Maintenance Costs: Remote diagnostics reduce the need for on-site visits by technicians, resulting in lower travel and labor costs.
- Predictive Maintenance: By analyzing historical data, AI systems can predict when equipment is likely to fail, allowing for proactive maintenance.
- Enhanced Safety: Remote diagnostics can be used to monitor and manage equipment in hazardous or hard-to-reach locations, improving safety for maintenance personnel.
- Global Reach: Organizations can access and manage equipment across multiple locations or even worldwide from a centralized hub.
- Data-Driven Decision-Making: Real-time data analytics provide valuable insights into equipment performance, enabling data-driven decision-making and process optimization.
Applications Across Industries
Remote diagnostics and troubleshooting are applicable across various industries:
- Manufacturing: In manufacturing facilities, remote diagnostics help monitor and optimize production lines and machinery.
- Energy: In the energy sector, remote diagnostics are crucial for monitoring and maintaining power generation, transmission, and distribution systems.
- Aerospace: Airlines use remote diagnostics to monitor and troubleshoot aircraft systems in-flight or on the ground.
- Healthcare: Hospitals rely on remote diagnostics for the maintenance and monitoring of medical equipment.
- Oil and Gas: Remote diagnostics are used to monitor and maintain drilling equipment and pipelines in remote and challenging environments.
Challenges and Considerations
While remote diagnostics and troubleshooting offer numerous benefits, challenges include data security, connectivity reliability, and the need for specialized training for personnel handling remote operations.
Remote diagnostics and troubleshooting are revolutionizing industrial automation by offering efficient, proactive, and cost-effective ways to manage and maintain equipment. As technology continues to advance and connectivity becomes more robust, the role of remote diagnostics in industrial automation will only become more central, ensuring higher uptime, improved reliability, and reduced operational costs for businesses worldwide.
The future of industrial automation spare parts is marked by innovation and efficiency. Predictive maintenance, 3D printing, IoT integration, AI-driven management, blockchain traceability, and remote diagnostics are among the trends and technologies shaping this sector. As companies continue to adopt these advancements, they can expect reduced operational costs, increased uptime, and enhanced reliability in their industrial automation systems. Embracing these trends will be crucial for staying competitive in the rapidly evolving landscape of manufacturing and automation.